The pharmaceutical industry is subject to very strict standards.
The slightest manufacturing defect can result in risks for patients, a potential health scandal with repercussions on the finances and reputation of the manufacturer or, at a minimum, stop or slow down production.
This is why the regulations set rules and good practices for controlling contamination at different stages of the production cycle.
Positioned towards the end of the production process, before final packaging, pharmaceutical visual inspection is an important control step to reduce the risk of particulate or cosmetic contamination, verify the integrity of containers and guarantee maximum patient safety.
What does the pharmaceutical visual inspection operation consist of? How does it take place in practice?
In this article, we answer your questions about visual inspection and present the pharmaceutical visual inspection solutions offered by STERIGENE.
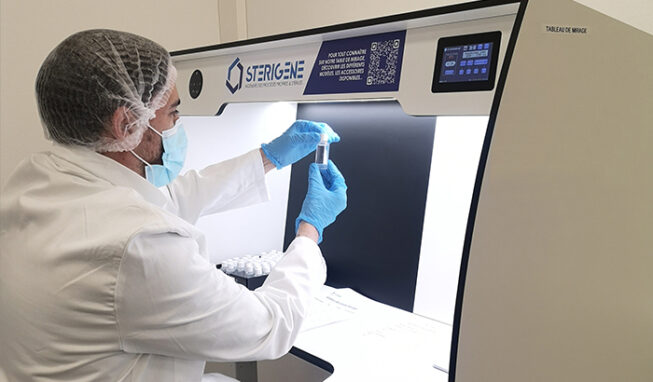
What is the visual inspection?
The definition of visual inspection
Visual inspection refers to an operation to check the absence of visible particles in pharmaceutical product containers.
It aims to reduce the risk of particulate and cosmetic contamination and to ensure the integrity of containers in order to guarantee better safety for patients. Concretely, visual inspection must make it possible to prevent the injection of a contaminated product into the human body.
The operation therefore applies to all injectable (parenteral) medications. Indeed, the materials used for the packaging and administration of parenteral medications are identified as a potential source of particulate contamination, whether:
- Glass or plastic used for containers
- Rubber used for closures
According to the European Pharmacopoeia, particulate contamination refers to the presence of undissolved, mobile foreign particles other than gas bubbles, unintentionally found in solutions.
Injecting a contaminated product puts the patient at risk of:
- Thromboses
- Embolisms
- Heart attack
- Stroke
- Death
- Infection
- Inflammation
Given these risks, the main international pharmacopoeias make visual inspection obligatory. However, they have differences. The European and British Pharmacopoeias state that injectable solutions, when examined under appropriate conditions of visibility, should be “clear and practically free from particles.” The U.S. Pharmacopoeia states that they must be “substantially free from particles” that may be observed upon visual inspection.
In all cases, visual inspection is subject to very high variability, because it is a subjective control carried out by an operator.
3 different solutions for visual inspection
Depending on the production rates and the financial means of the manufacturer requiring equipment, there are 3 different visual inspection solutions:
- Manual visual inspection: the feeding of the product, the handling and the visual inspection are carried out by an operator.
- Semi-automatic visual inspection: feeding and handling are automated. The inspection is carried out by an operator.
- Automatic visual inspection: the entire operation is done automatically.
The principle of operation of pharmaceutical visual inspection
What can be inspected?
All parenteral products are subject to visual inspection. Pharmaceutical glamor covers several types of containers:
- Light bulbs
- Bottles
- Micro vials
- Cartridges
- Syringes
- Bottles
For its part, the product can be in the form of:
- Liquid (translucent aqueous, viscous/oily, suspension)
- Solid (lyophilisate cake, powder)
The visual inspection operation will make it possible to visually observe defects:
- Particulates (inside the container)
- Cosmetics (outside the container)
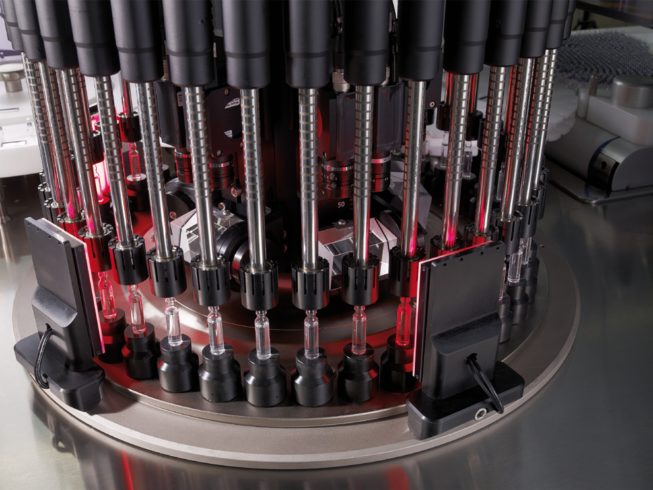
The light response of contaminants
Pharmaceutical visual inspection aims to visually detect contaminants. To do this, the visual inspection solutions will subject the visual inspected products to a high light intensity.
Indeed, contaminants can have different responses to light. Some absorb light while others reflect it.
The machine combines the advantages of different lighting techniques to detect the widest range of particles:
- Polarized light for fibers
- Light stripe Projection: projection of a laser on the object to scan the surface allowing the shape of the particle to be reconstructed
- NIR/RX for bubbles
We can also play with the backgrounds depending on the type of particles to be detected. A black background makes it easier to detect reflective particles (by reducing light reflections on the glass). A white background, on the other hand, promotes the detection of other particles (by providing more brightness to the product).
Cameras
Depending on the containers and types of products for which we seek to detect potential contaminants, we will use different types of cameras.
The linear camera allows you to recreate an image line by line using a 1xn pixel sensor (a line of pixels). It responds to use cases for opaque solutions or cosmetic defects.
For transparent liquids and particles, a matrix camera will be used. It allows you to obtain a sequence of images. The pixels that make up its sensor form a matrix of size nxm (with n and m > 1).
Pharmaceutical visual inspection recipes
Here again, the recipes vary depending on the types of products to be visually inspected.
For suspensions or turbid products, the recipe will be as follows:
- Product homogenization
- High rotation speed to stick particles to the walls
- Projecting side light to increase contrast
- Linear cameras for high precision
In the case of high density suspensions, several stations can be set up to subsequently establish a correlation.
For very viscous products (for example, hyaluronic acid), we would rather use this recipe:
- Analysis of the trajectory to determine the apparent speed
- Reliable detection through impressions and occlusions
- Robust determination of particle size and shape
Finally, we can use Methylene Blue to detect particles up to 50-100µm.
False positives and false negatives
The inspection is likely to generate false negatives or false positives depending on different influencing factors:
- Glass surface quality
- Optical density of suspensions
- Air bubbles generated by operating conditions (conveying of units, temperature of solutions favoring their degassing during inspection)
If in doubt, it is best to re-evaluate the inspection performance.
Pharmaceutical visual inspection solutions offered by STERIGENE
At STERIGENE, we offer several pharmaceutical glazing solutions to meet your contaminant detection needs:
- CleanView visual inspection tables, developed and manufactured in France by STERIGENE
- Easy or Plus automatic inspection machines
- PWL semi-automatic visual inspection machines
The ARGO, EASY, PLUS or PWL pharmaceutical visual inspection machines are developed by our partner OPTREL (STEVANATO Group).
Do you have contaminant detection needs?
Our teams support you in choosing a visual inspection solution in line with your uses and your budget.
We offer both solutions developed internally or offered by our partners.
A project ? Discuss it with one of our experts or download our explanatory brochure.
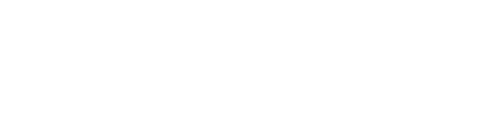