For drug manufacturers, protecting products and operators against contamination is a major issue.
The slightest doubt about the integrity or sterility of a batch has serious consequences:
Financial, with the destruction of the incriminated batch and the temporary shutdown of the production line concerned.
Human, sanitary if contamination is not detected in time
On brand awareness
Contamination control also occupies a large place in pharmaceutical GMP (good manufacturing practices).
Barrier technologies (RABS, isolators) meet these challenges. These are safety devices used to protect medicines and pharmaceutical products from contamination and unauthorized manipulation. Their aim is to guarantee the integrity and quality of pharmaceutical products, the protection of patients against potentially dangerous or altered medicines as well as the protection of operators.
In this article, discover how these technologies work, illustrated by 3 use cases.
What is barrier technology?
The definition of barrier technologies
In the pharmaceutical industry, good manufacturing practices (GMP) particularly emphasize the implementation of good practices to avoid contamination. Barrier technologies aim to ensure the protection of sterile production and the management of incoming and outgoing flows.
Concretely, a barrier technology designates a system allowing the process to be separated from the operator in order to:
- Avoid cross contamination
- Separate the space (separate exhaust air/waste exhaust)
- Protect operators in the case of toxic products/containment
- Protect the product
- Allow class skips
Barrier technologies include isolators and RABS.
What is an insulator?
Still according to EU GMP, an isolator means “a decontaminated unit supplied with air quality class A (ISO 4.8) or higher, which offers continuous and flawless isolation of its interior environment from the exterior environment ( i.e. personnel and air present in the immediate controlled atmosphere environment). »
An isolator is an enclosed space, designed and used to prevent product or equipment from being exposed to the room environment.
Materials can be introduced into a closed system, but any additions must be made in a way that avoids exposure of the product to the room environment (for example, through sterile connections or fusion systems).
It may be necessary to open a closed system (for example, to install a filter or make a connection), but it must return to its closed system status through a decontamination or sterilization operation before use.
What is a RABS?
The RABS (Restricted Access Barrier System) is a combined system of physical (rigid) barrier and aerodynamic protection around the critical area.
Depending on the level of protection needed in your context and other criteria such as the performance of your HVAC (or HVAC: heating, ventilation and air conditioning) system, you can opt for different types of RABS.
In a passive RABS, the HEPA filters are part of the zone. This implies that your HVAC is sufficiently efficient in terms of flow speed and filtration level.
The RABS is said to be active when the HEPA filters are part of the machine.
We speak of open active RABS when the system is open in the lower part with air release and recirculation in the customer HVAC system.
On the other hand, in the context of a closed active RABS, the system is closed with integrated air recirculation. In other words, the air still remains in the system and does not recirculate through your HVAC.
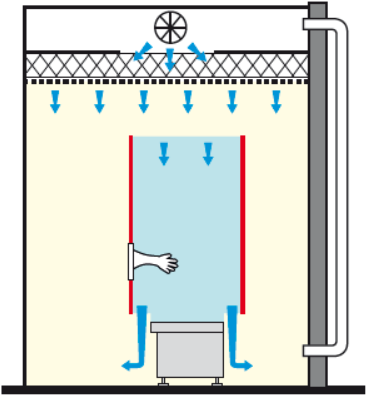
RABS PASSIVE OPEN
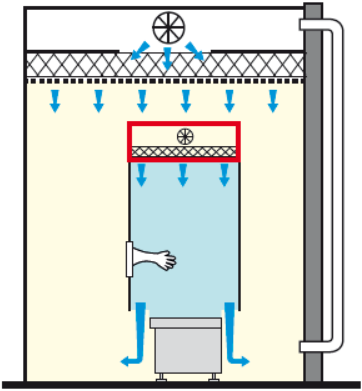
RABS ACTIVE OPEN
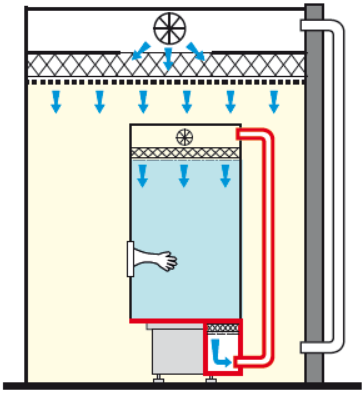
RABS ACTIVE CLOSED
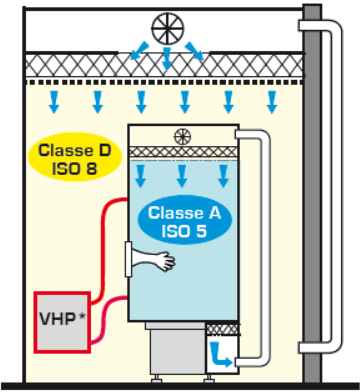
ISOLATOR
In what cases are barrier technologies used?
The EU GMPs specify the use cases for barrier technologies.
They are mandatory for:
- MTI: Innovative Therapies Medications (gene therapy, patient immune deficiency)
- Viral vectors
- GMOs
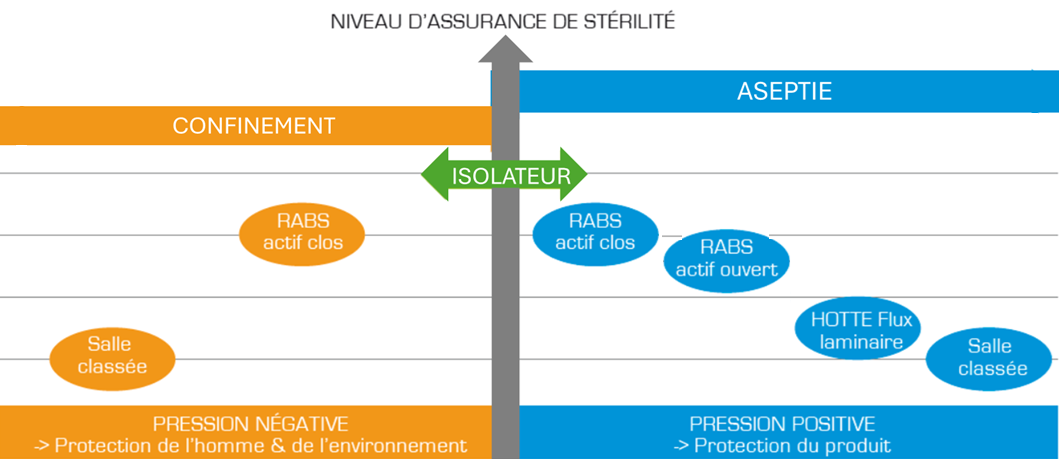
Barrier technologies are used in production (aseptic filling, particularly for injectable products) and in quality control.
Depending on the criticality of the product, a more or less closed system will be used. The more we move towards a closed system, the higher the level of sterility assurance will be.
In addition to protecting products, barrier technologies also aim to protect operators, via containment measures. Here too, this dimension impacts the choice of one or the other system.
In practice, the process starts with a risk analysis. The manufacturer must be able to justify its choices to the Medicines Agency. The manufacturer must obviously take into account the financial and human risks, in terms of notoriety, in the event of doubt about the integrity or sterility of a batch.
3 use cases for barrier technologies
Case #1: FCTS – FEDEGARI sterility test isolator
In this first example, the equipment is used to carry out sterility tests on samples from production lines, as part of quality control. The aim is to demonstrate, statistically, that the entire batch is indeed sterile.
According to the isolator principle, the space is separated from the operator. It is equipped with gloves to avoid manipulation by and for the operator.
The system allows decontamination with H2O2 of the entire chamber to work in sterile conditions. It is equipped with an airlock for the entry and exit of equipment. The airlock allows the material to be decontaminated before entering the isolator itself.
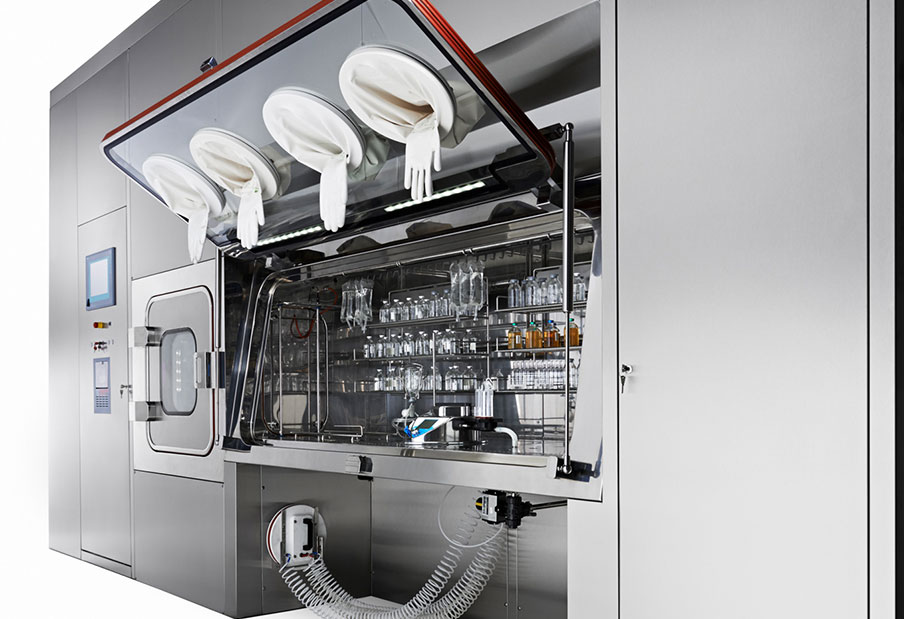
Case #2: IPSEN
Here, in the case of IPSEN, the isolator intervenes in the context of hormone production and, more precisely, at the filling stage. The main challenge is to protect the operator from the product, whose active ingredient is extremely powerful. To do this, the system must allow confinement to be maintained throughout the process.
The equipment has been designated for:
Maintain the leak level below 1% vol/h
Meet ISO 14644: 3 classification
Present a chamber pressure of +50Pa +/-10Pa ISO8
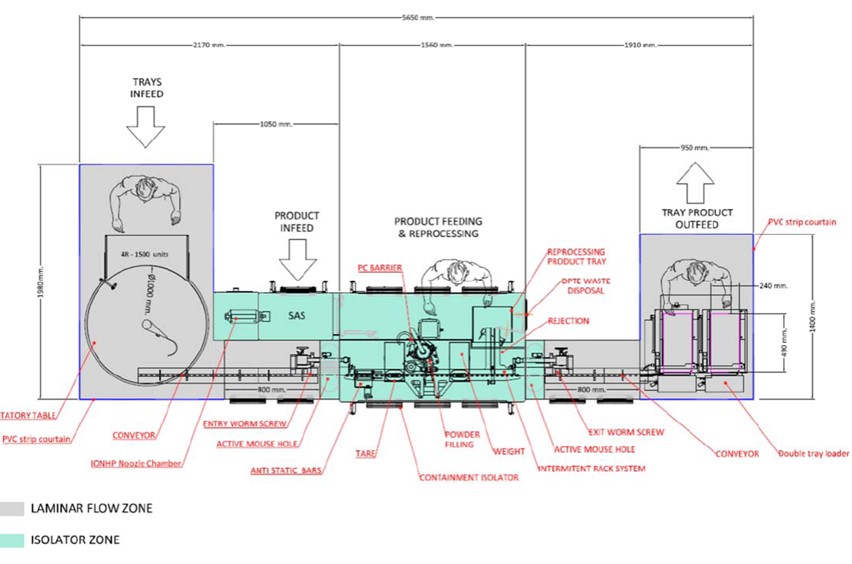
This system presents a hybrid operation with:
- An isolated area (in green on the diagram) when in the presence of the product
- A laminar flow zone (in gray) for the entry and exit of the material, with a lower level of confinement
The system plays very finely on aerodynamic parameters to maintain the desired level of confinement from one zone to another, in an environment generally in depression. Air barriers, placed between the compartments, make it possible to maintain the pressure differential between neighboring compartments.
Case #3: Central Pharmacy of the Armed Forces
The third case corresponds to a production line that involves several types of containers: cartridges, syringes, vials.
The PCA production line is L-shaped with a series of compartments. Between them, these compartments are linked by a pressure cascade.
The insulator will ensure the sterility of the product precisely because manufacturing takes place in an overpressure environment which protects it from external contaminants.
In this system, certain compartments will be used specifically depending on the type of container to be produced.
You have carried out your risk analysis and you are looking for the ideal solution to maintain the asepsis of your pharmaceutical products.
Arbitrating between level of protection, budgetary cost and potential risks is not always easy. Depending on your production challenges and the criticality of the products concerned, you do not necessarily need a homogeneous level of containment in all the compartments of your production line.
Our experts help you choose the barrier technologies adapted to your situation.
A project ? let’s talk about it
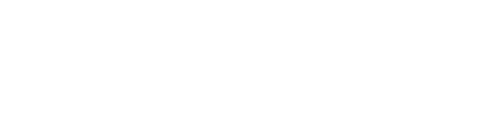