In drug manufacturing, production takes place in controlled environments. The objective is to maintain the quality, safety and effectiveness of the medicines produced by minimizing the risks of contamination.
In these environments, levels of airborne particles are strictly controlled. Manufacturers also design and monitor controlled environments to minimize the presence of microorganisms and bacteria, including through rigorous cleaning and disinfection procedures.
The EU GMPs define the good practices to be put in place for manufacturers. Biocleaning appears to be a critical production step to eliminate waste and particulate, biological and chemical contaminants deposited on surfaces. In the overall biocleaning process, ASD (airborne surface disinfection) contributes to disinfection. The reform of Annex 1 of good manufacturing practices even makes it an essential element.
In this article, you will discover what ASD is and its importance in complying with GMP. We also present Stérigène solutions in terms of ASD.
ASD, a key element of biocleaning
The goal of biocleaning
Biocleaning consists of restoring cleanliness to equipment or premises:
- Following production anomalies (emergency activity)
- Between 2 batches or according to a planned schedule (planned activity)
It brings together a series of steps aimed at eliminating/reducing contaminants in the production environment to:
- Obtain visually clean surfaces
- Make the particle load acceptable according to the class of the zone
- Make the microbial load acceptable according to the class of the zone
“Acceptable” particulate and microbial concentrations are defined in Annex 1 of EU GMP, updated in August 2022.
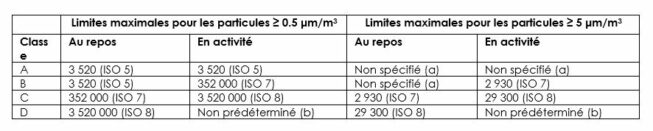
In accordance with GMP, the manufacturer is required to carry out continuous monitoring of its production environments to keep contamination below the thresholds corresponding to the defined class.
A production stage supervised by GMP
The revision of Annex 1 of GMP requires manufacturers to:
- Adopt a clear and concise contamination control strategy
- Adopt a defined quality system based on the principle of Quality Risk Management
In other words, the manufacturer must assess the risks inherent in its production environments and processes, then implement means to reduce these risks. To this end, GMPs provide guidelines to help stakeholders identify, scientifically evaluate and control all potential risks during the process.
Compared to the previous version of GMP, the revision of Annex 1 increases the requirements for biocleaning. To become compliant, we now recommend following 8 steps:
- Roughing: Removal of visible manufacturing waste to facilitate subsequent cleaning
- Dust removal: particle and chemical decontamination by vacuuming or wet sweeping
- Washing/detergency: possible use of detergents to separate contamination from the surface
- Rinse with PPI water when using detergents to suspend residues
- Scraping: mechanical action to remove residue
- Disinfection to eliminate/reduce microorganisms
- Rinse with PPI water if necessary
- Scraping if rinsing to eliminate disinfectant residues
What do GMPs say about disinfection?
The revision of Annex 1 of GMP provides clear guidance on disinfection expectations.
Article 4.33 provides several clarifications:
- Disinfection must be based on a formalized program
- Prior cleaning should be carried out to remove surface contamination
- More than one type of disinfectant agent should be used
- Disinfection should include periodic use of a sporicidal agent
Further on, the text provides important additions. The process must take into account the appropriate contact time and the manner and surfaces on which the disinfectants are used. Regular monitoring is expected to ensure the effectiveness of the process. And cleaning programs must effectively remove disinfectant residue.
Finally, for the first time, DSVA is explicitly cited in the text as good practice in disinfection.
Why and how to implement ASD?
What is the DSVA?
Aerial surface disinfection is an automatic process aimed at the homogeneous disinfection of all surfaces in the target area. By disinfection we mean the operation with the temporary result of destroying, eliminating or slowing down the development of micro-organisms and/or inactivating unwanted viruses.
ASD consists of dispersing a biocidal product (disinfectant) in the form of gas, vapor and/or aerosol from a dedicated device. It targets surfaces and not the air. It does not require human intervention.
In the process of bringing an area back into compliance, disinfection is the final step before qualifying a clean room. It comes after manual cleaning. It must be carried out carefully and requires full validation.
ASD standards
ASD is a process governed by:
- A French standard: NFT 72 281
- A European standard: EN 17 272
These standards make it possible to verify the effectiveness of the diffuser/product couple through the logarithmic reduction achieved by the product. They also make it possible to determine the bactericidal, yeasticidal, fungicidal, sporicidal and virucidal activity of the process.
The EN 17 272 standard is an evolving reform of the NFT 72 281 standard. It is distinguished by:
- A stronger requirement in terms of distribution homogeneity
- Effectiveness against certain types of additional microorganisms
- Clearer testing requirements for enclosure volume
- The introduction of the concept of overall contact time of the disinfectant agent
Finally, the BPR biocide directive No. 528/2012 regulates biocidal products. It aims to harmonize and control the marketing of these products at European level.
The effectiveness of biocidal products is also standardized. It is governed by a European standard EN 14 885 which:
- Makes it easier for users to compare products
- Establishes standards that a biocide must meet to claim microbicidal activity
- Defines the standards to be passed according to the sectors of activity, applications and claimed efficiencies
HPE technology
ASD is based on a machine/product pair that cannot be modified. The HPE technology we offer to our customers combines an H2O2 solution and a ZHEROX mobile device that can be networked to process larger volumes.
Control of the ZHEROX machine can be triggered remotely via a dedicated application which allows the device to be managed and activity reports to be collected.
Thanks to this technology, a solution of hydrogen peroxide (H2O2) with a concentration of less than 8% is diffused into micro-droplets which then pass through a high-voltage electromagnetic field and undergo ionization. Disinfection is carried out by the action of free radicals. The electromagnetic field imparts an electrostatic charge to the dry fog, ensuring even dispersion on surfaces and leaving no residue.
HPE technology has several advantages:
- Effective on a broad spectrum of contaminants
- Timeliness
- Safety with respect to supports
It has obtained the BPR N°528/2012, NFT 72 281 and EN 17 272 standards.
In terms of performance, ZHEROX allows a reduction of 6 logs in 3 hours at a lower cost.
Disinfection is a key step in biocleaning. While the revision of Annex 1 of the GMP has strengthened the requirements in terms of contamination control and quality risk management, the DSVA is becoming essential.
By relying on HPE technology, you have a solution combining efficiency and competitiveness and in line with current standards.
Beyond technology, the Stérigène teams support you in developing your disinfection strategy (audit, advice, qualification, staff training, maintenance).
You want to know more ? Contact us to speak with one of our experts.
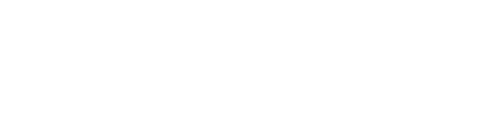