The pharmaceutical industry is subject to strict quality and safety standards to ensure the integrity and effectiveness of products entering the market. Regulations govern manufacturing environments and processes to avoid the risk of contamination.
Recent developments in Annex 1 of EU GMP further strengthen the guidelines relating to the control of contamination in production environments.
Initially, the text gave manufacturers until August 2023 to comply with the new requirements. Even if the first checks are not expected to take place before 2024, it is important for the stakeholders concerned to be ready.
In this context, biocleaning plays a crucial role in ensuring a production environment to limit the risks of contamination.
In this article, discover what biocleaning consists of and how it fits into the contamination control strategy and responds to the challenges of room cleanliness.
What are the characteristics of a clean room?
What is a cleanroom?
A cleanroom is a controlled environment specially designed to maintain a high level of cleanliness and contamination control.
Cleanrooms and related controlled environments provide means to control contamination of air and, where applicable, surfaces to levels appropriate for contamination-sensitive activities such as the aerospace industry, microelectronics, the pharmaceutical industry, medical devices, health, the food industry, etc.
Qualification of cleanrooms
The ISO 14644 standard establishes guidelines for the classification and monitoring of clean rooms.
It divides clean rooms into classes based on the concentration of particles per volume of air. Each cleanroom class has specific ceilings for particle concentrations per volume.
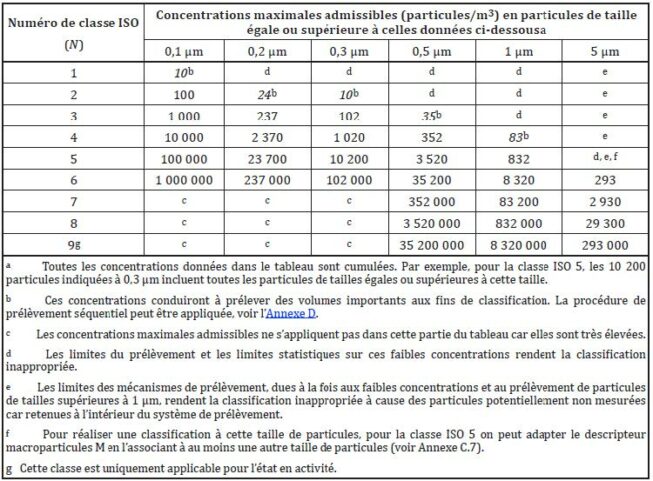
Qualification of cleanrooms in pharmaceuticals
Cleanrooms are used primarily in the manufacturing of sensitive pharmaceutical products, such as sterile drugs, medical devices, and other products sensitive to microbial and particulate contaminants.
In this context, the qualification of clean rooms depends on the particle and microbial concentrations defined in the GMPs. For the production of sterile medicines, the limits are defined in Annex 1 of the EU GMP, updated in August 2022.
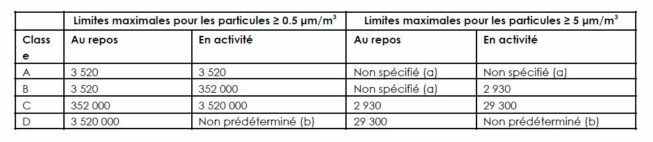
Once the clean room has been qualified, the manufacturer must implement monitoring to maintain the appropriate level of cleanliness.
Biocleaning, the ultimate step towards a clean environment
What are the steps to maintain cleanliness requirements?
Traditionally, there are 3 types of contamination:
- Particulate contamination: inert particles, dust, fibers, waste, etc.
- Microbiological contamination or biocontamination: microorganisms and viable particles
- Chemical or molecular contamination: chemical contaminants, residues
Depending on the type of industry concerned, attention will focus more particularly on one or more types of contamination. In the pharmaceutical (or cosmetics) industry, cleanliness requirements are such that they concern microbiological, chemical and particulate contamination.
To maintain cleanliness requirements, contaminants and their contamination vectors must be eliminated or minimized. To do this, several elements must be taken into account:
- The design of the room: qualified AHU, overpressure room
- Isolation of production: barrier technologies, separation of material and human flows, etc.
- Limiting incoming contaminants: covering, entrance mats produced with low release, overpackaging of consumables, etc.
- Contaminant removal: overall process of eliminating or reducing any contaminant from an area, object or person
What is biocleaning?
The last step is called disinfection, and it consists of using biocidal products to destroy, or render harmless, harmful organisms, through chemical or biological action. Disinfection products can be:
- Sprayed on a suitable fabric
- Impregnated on site in a bucket
- Applied via a presaturated wipe
Although targeting harmful organisms, biocides are active products capable of having effects on humans, animals or the environment. Consequently, their marketing is governed by European regulations, called the Biocide Directive (BPR).
Regulatory implementation is divided into two stages:
- Evaluation of biocidal active substances, leading or not to their approval
- Evaluation of products containing them with a view to obtaining a marketing authorization (AMM) only in the country which issued the authorization
The stages of biocleaning
Biocleaning encompasses a set of steps and processes aimed at removing microbial, chemical and particulate contaminants from surfaces and equipment in pharmaceutical production areas.
In the fundamental protocols, to eliminate all types of contaminants, 4 steps are necessary. However, developments in Annex 1 of EU GMPs raise the level of requirements. To become compliant, we recommend following 8 steps:
- Roughing: removal of visible manufacturing waste to facilitate subsequent cleaning
- Dust removal: particle and chemical decontamination by vacuuming or wet sweeping
- Washing/detergency: use of detergents to separate contamination from the surface
- Rinse with PPI water when using detergents to remove residue
- Scraping: mechanical action to eliminate residues
- Disinfection to eliminate/reduce microorganisms
- Rinse with PPI water if disinfectant with residue (quaternary ammonium)
- Scraping if rinsing to eliminate disinfectant residues
Base & Accessories of the CLEANVIEW® candling table
To comply with EU GMP Annex 1, all steps of the biocleaning process must be documented, including the chemicals used, application times and method of control.
As an industrialist, you have an obligation to achieve results: to remain below the contamination thresholds corresponding to the cleanliness class required for your production environment.
In sterile, you are required to validate that biocleaning has been effective but you are free to establish the protocol that will best allow you to meet this objective while taking into account your uses and your production constraints. The frequency of biocleaning can therefore vary from one manufacturer to another.
Likewise, the choice of products will vary depending on criteria linked to the protocol you have defined. Their effectiveness is validated by European standards, which has the advantage of easily comparing biocides with each other. These standards are defined according to use and sector of activity.
The conditions of application are just as important and their effectiveness results from the combination of four factors (each accounting for 25% in the effectiveness of a decontamination operation) which constitute the Sinner circle:
- Temperature, which improves the solubilization of contamination
- Mechanical action: combining different tools, notably the choice of cleaning fabrics
- Chemistry: the product must be chosen to eliminate contaminants, not damage surfaces and minimize the risk of residues
- The obligatory contact time between microorganisms and biocidal products to eliminate them
In addition, regulations require manufacturers to carry out a risk analysis which involves qualification of suppliers. Therefore, choosing a recognized supplier for your biocidal products is preferable. For our part, we work in partnership with the manufacturer Christeyns (Klercide range).
Biocleaning is an essential step to maintain clean room requirements and reduce the risk of contamination in your production environments.
Developments in Annex 1 of EU GMP require raising the level of requirements for decontamination operations, with the addition of additional steps in the biocleaning process.
To do this, STERIGENE supports you both in defining your biocleaning protocols and in the choice of fabric products, biocides and cleaning accessories, adapted to your activity, your uses and your constraints.
Do you have questions about biocleaning issues? Contact us to speak with one of our experts.
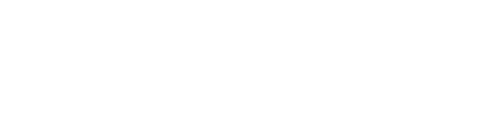