EFFICIENCY & EFFECTIVENESS OF cGMP WASHING
The efficiency of a cGMP wash results from the chemical actions of the product used, breaking the links between the support load and its soiling, and mechanical, the rinsing removing the dirt.
The effectiveness of each action is proportional to the duration of exposure to the treatment, but they are inversely proportional to each other: the more intense the chemical action, the less powerful the mechanical action will be for the same cleanliness assurance threshold. and reciprocally.
Chemical action: wetting, soaking, immersion, sprinkling, spraying, dissolving, etc.
Mechanical action: wiping, brushing, friction, blowing, suction, projection, etc.
cGMP washing is an essential operation in the manufacturing cycle of active ingredients and pharmaceutical products. Any process evolves between a level of assurance of cleanliness and a level of acceptance of contaminants.
Also the recommendations or even legal obligations of GMP or GMP, particularly with regard to the minimum qualities of water usable in the processes, strictly governing cleaning operations must be understood and integrated into the design to choose the appropriate techniques and materials.
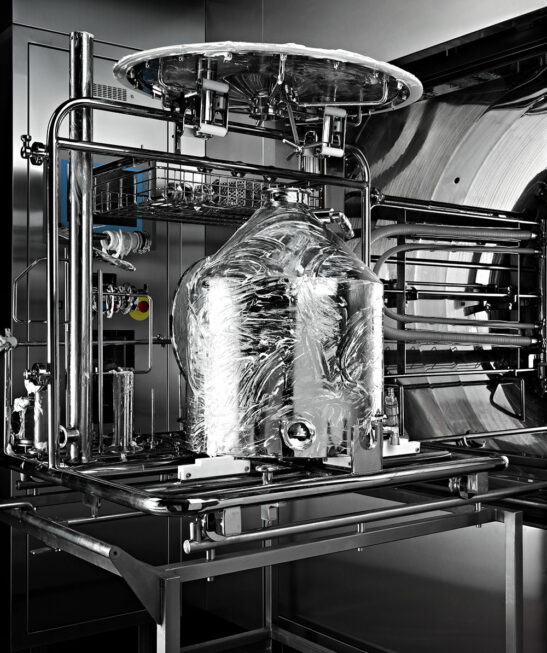
cGMP WASHING OPTIMIZATION
Optimization of chemical and mechanical actions will be obtained thanks to know-how and work on fundamental parameters such as concentration, temperature, flow rate, time and reproducibility.
The choice of a washing method must be made based on the input data (detailed description of the soiling) and the output data (required requirements, quantifiable results, etc.). Based on this data, it will be necessary to consider the appropriate means and move towards optimization of efficiency parameters.
First of all regarding the technologies: High and Low Pressure pharmaceutical washer Mechanically, friction is influenced by the pressure, the angle of attack and the abrasion ratio at the interfaces.
The higher the pressure, the lower the flow rate (for economic reasons).
The greater the flow, the less the pressure will be (more traditional).
Today 80% of industry processes are at low pressure but in recent years the proportion at high pressure has continued to increase.
At the level of production procedures and routines: Manual procedures and automatic programs (number – duration – sequences of successive phases, etc.)
In terms of equipment design: Pharmaceutical washers either static or mobile for Cleaning In Place (NEP=CIP) Cleaning In Place
In terms of the quality of the means implemented: Finishes ensuring reproducibility (geometry, assembly, sealing) or even inclination, dead arms, etc.
This allows you to choose the most suitable equipment…
Our dedicated, very pragmatic training modules allow you to tackle washing and drying issues with confidence, from design to qualifications.
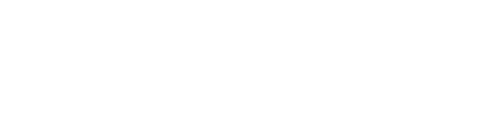